

Instrumentation and control terminology
It is necessary to measure, control and maintain constants some magnitudes such as: pressure, flow, level, temperature, pH, conductivity, etc, which means that you have to know all terms to use for such actions.
SENSOR:
The word is used by extension a whole series of devices and devices.
However entering more in detail it can be said that the sensor itself is the primary element of measurement.
In the case of a flow measurement for example it can be a plate orifice, venturi, nozzle, turbine, etc.
As seen, the primary element or Sensor takes a certain magnitude that pulls out of the process and consequently gives us another physical magnitude that we can Take advantage to get the information we want that is ultimately the measurement.
TRANSMITTER:
It is known as transmitter in the field of instrumentation and control to the signal conditioner set, in cases integrated to the sensor and in others as an independent device connected to the sensor by electric conductors, pipes etc.
TRANSDUCTOR:
It is the instrument or device capable of transforming the available energy into a physical magnitude given in another magnitude, physical that the system can take advantage of to realize its objective of measurement and control.
Are used for example to move from magnitudes conditioned in pressure to current or voltage and modern to digital variables for field buses.
It could also be called transducer to the transmitter Sensor assembly, since it takes the magnitude of the process and translates it to a normalized variable for the control system.
We note that the conditioning Linealiza, compensates the drifts by temperature of both sensitivity and zero etc.
RANGE:
It is the set of values between the limits (upper and lower) that is capable of measuring the instrument to which we refer, within the limits of accuracy indicated for it. indicated by the above and below values.
RESOLVE:
It is the least change in the process variable capable of producing a perceptible output in the instrument. It is generally expressed as a percentage of the instrument's upper measuring limit (in-depth scale value).
ERROR:
It is defined as the difference between the measured value and the true value. The error has in general varied causes.
which can in some way foresee, calculate, eliminate by calibrations and compensations, are called deterministic or systematic.
Those that cannot be foreseen, because they depend on unknown causes, or stochastics are called random.
ACCURACY:
Ability of an instrument to give small error values.
If an instrument is correctly calibrated unavoidable random errors will cause the measurement results to have a certain dispersion, if the average of the measurements coincides with the true value the instrument is accurate.
The statistic (mean in this case) can bring us closer to the real value.
The accuracy can be specified as a percentage of the measured value or as a percentage of the instrument's in-depth scale value.
In the case of instruments intended for industrial processes in general, this specified accuracy corresponds to the entire measuring range of the same.
PRECISION:
The greater the lower precision is the dispersion of the measurement values around the measured value.
could happen that this value was not exact but the dispersion to be girl, in that case the instrument is precise but not exact.
Accuracy is associated with statistics such as variance and standard deviation.
In the technique it is usually demanded that the values of variables important for the quality of the product are kept within a field given by three standard deviations in more or less of the specified value, and these deviations must be small to have good precision.
REPEATABILITY:
Ability of an instrument to repeat the output when the measurement is reached on several occasions under exactly the same conditions.
A very important detail of this is that it must be demanded that the measurement should be carried out with the variable in a growing or decreasing direction but not in both directions, since in that case it ceases to be repeatability to be hysteresis.
As other instrument specification parameters, it is customary to specify repeatability as a percentage value of the measurement or the instrument's scale background.
HYSTERESIS :
The damping plus the frictions means that there is an energy consumption in the loading and unloading of the instruments.
is due to that the upward calibration curve does not coincide with the descending and that is called low hysteresis.
Hysteresis is the ability of an instrument to repeat the output when the measurement is reached on consecutive occasions under the same general conditions but once with the measurement of the variable in one direction (for example increasing) and in the following with the Variable in the opposite direction (for example decreasing).
As other instrument specification parameters, it is customary to specify hysteresis as a percentage value of the measurement or the instrument's scale background.
INTERCHANGEABILITY:
When reference is made to the inter-changeability of instruments, several aspects may appear.
With respect to accuracy, if an instrument of/-1% is replaced by another one with the same exactness, given that the errors can be added under certain conditions, when making the change we will say that we can assure the measurement in/-2%, if we do not take precautions Special calibration.
There are however industrial aspects such as: chemical compatibility of the materials.
Communication System or instrument standard compatibility.
Others are saveable with adaptations such as physical connections to the process.
CALIBRATION:
A calibration of the instrument is a set of values of the relationship between the input variable (of the process) and the output variable (measurement), where the remaining constant conditions are maintained.
As we see there will be infinite calibrations if we vary the conditions in which the curve is lifted.
This is some way of obtaining expressions that relate the external variables that influence the obtaining of the measurement in order to correct the calibration in standard conditions. A typical example is the temperature as a variable that causes the measurements of other parameters in process control to derive.
with the advancement of the digital age, you can store several calibrations and give the measurement through interpolation routines between them.
SENSITIVITY:
It is the variation in the output of the instrument by unit of variation of the variable of the process (input), in short it can be said that it is the gain of the instrument.
The ideal is that it remains constant. In general the primary elements are derived from the sensitivity with other variables, basically the temperature, so the signal conditioning that makes the instrument should be responsible for compensating those drifts.
In many industrial instruments it is also measured at the temperature to make this compensation.
SENSITIVITY ERROR:
As we have mentioned the temperature in general produces a drift or variation of the sensitivity of the primary element. To a large extent this drift is compensated by the electronic signal conditioning system of the instrument.
The different primaries have a variable output depending on the temperature. In general this characteristic is specified by the so-called temperature coefficients. When these coefficients are deepened, instead of being constant, they can be polynomials temperature function of varying degrees.
ZERO ERROR:
Even if the value of the process variable is at the minimum of the range, where the output of the instrument must be the value associated with the zero of the range (in current for example 4mA), the instrument marks its output a non-zero value.
That value is the zero error. In general, there are systems to annul, or to compensate for the error of zero, these systems can be adjustments by means of movements in the instrument or by software.
LINEARITY:
In classical control linearity is taken as a requirement since the whole theory is based on that type of system dynamics (linear differential equations).
Although this has been overcome the lack of linearity always represents complications so: the linearity of the instruments of measurement and control is always a characteristic sought.
If the process is slow with respect to the dynamics of the instrument one can think that it is set in the measurement value at a much higher speed than the changes that the measured variable can make.
In these conditions it may be considered that the instrument has a static alinealidad i.e. I do not consider its dynamics.
So I can have a calibration curve raised in static conditions and use it to compensate for the alienealiades of the instrument.
In practice the compensations of the signal conditioning system will greatly eliminate errors by Alinealidad, but in a certain persist, and are usually expressed in percentage value of the maximum deviation from the linear output The entire range of the instrument with respect to the value of the scale of the tool.
DYNAMIC RESPONSE:
The instrument response diagrams at variable input frequencies traversing the entire spectrum presented in logarithmic form (Bode diagrams) give a finished idea of the instrument's ability to respond with a reasonable output magnitude ( Constant gain) and without a notable phase lag.
Note that phase delay tends to instabilize the control loops.
to the frequency range where the above conditions are met is called "bandwidth".
Obviously if the signals to be measured are of very low frequencies will not interest the characteristic of the dynamic response of the instrument.
In processes where the time constants of the transfers are large with respect to those of the usual instruments there is no need to worry about the dynamic response of the same. In control of servomechanisms, space science, robotics etc. The importance of these characteristics begins to appear.
STABILITY:
The stability of the calibrated accuracy is specified as a guarantee of performance, and influences the price, for example 1% or for 5 years or 10 years.
It is interesting to point out that it refers to 1% of what is spoken. In general it refers to the accuracy throughout the entire range of the instrument (accuracy) and can be specified as already mentioned in respect of L measured value (or of reading) or of the scale of the instrument (OFS of full scale)
TRANSDUCER ACTIVE – PASSIVE:
It is said of a transducer that is passive when it is not fed from another source other than that of the same process that it is measuring. Instead the asset is one that generally needs less energy from the process itself to measure as it has for its operation an external source.
Deflection instrument:
In the instruments of deflection the variable that activates the instrument works against an antagonistic effect until the equilibrium found indicates how much the measured variable is worth.
Instruments of BALANCE or null deflection:
The variable that activates the instrument is compensated with a mechanism or internal circuit until the balance found achieves null deflection.
The value of the necessary amount of compensation to get the null deflection gives the measured value, in general this method can be more sensitive because it always works in the environment of zero
The accuracy of the deflection instrument depends on the calibration of the physical medium that is deflecta, (spring or similar).
The instrument back to zero or null deflection is generally more accurate and works against the pattern directly. The disadvantage of balancing measuring methods around zero appears in dynamic measurements when it is not possible to waste a lot of time to perform the rolling, with the application of fast electronic systems this is feasible in increasingly demanding measurements .
Desired entries:
Are the inputs to the measurement system of the physical variables that we want to measure.
Non-linearity:
Maximum deviation from the calibration curve with respect to the straight line by which it has been approximated.
Measurement field:
Range where you can make the measurement between the limits. E.g: thermometer designed to measure between range-20 ° and 60 ° being the measurement field.
scope, or scale background:
The difference between the upper and lower limits. (X-axis). E.g: the scope would be 60 °-(-20 °) = 80 °.
Full scale output:
Difference between the maximum and minimum output of the measurement field. (Y-axis).
DRIFT:
Variation depending on the physical variables. e.g: normal wear and tear over time.
SATURATION:
The maximum input level through which the sensitivity decreases.
REPRODUCIBILITY:
If an instrument has this feature, it is making sure that it will give us the same result even though the factors vary over time.
DYNAMIC ERROR:
Is the difference between the indicated value and the exact value of the measured variable, the static error being null.
Unit of Measure:
Measurement of the process and direct contact with the control variable (meters and sensors).
UNIT OF CONTROL:
Processor component that directs and coordinates most operations on the computer (computer, PLC and microcontrollers).
Control end Element:
A mechanism that alters the value of the manipulated variable in response to an output signal from the automatic control device (actuators, switches, motors, valves, double-acting cylinders, etc.).
CURL:
Open loop: Measurement and evaluation without modification.
Closed loop: they are measuring and evaluation with final modification.
CONTROL MODES:
-
On/off
-
Proportional: A Greater amount of error, greater amount of control.
-
Integral Proportional: The control action is carried out on the accumulated error.
-
Derivative proportional: The control action happens with respect to the rate of change of the error (anticipated).
-
Proportional + Integral + derivative.
EFFICACY:
Few resources to achieve anything. Therefore it can be said that the efficacy is that capacity or quality to achieve, to work or to obtain a particular result, enjoying the virtue to produce the desired effect.
EFFECTIVE:
Use of any resource to achieve it. It is the one that is assigned a responsibility and this fulfills it following the guideline established in the Compendium of norms or contract that it signed when the working relationship was agreed.


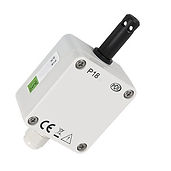
